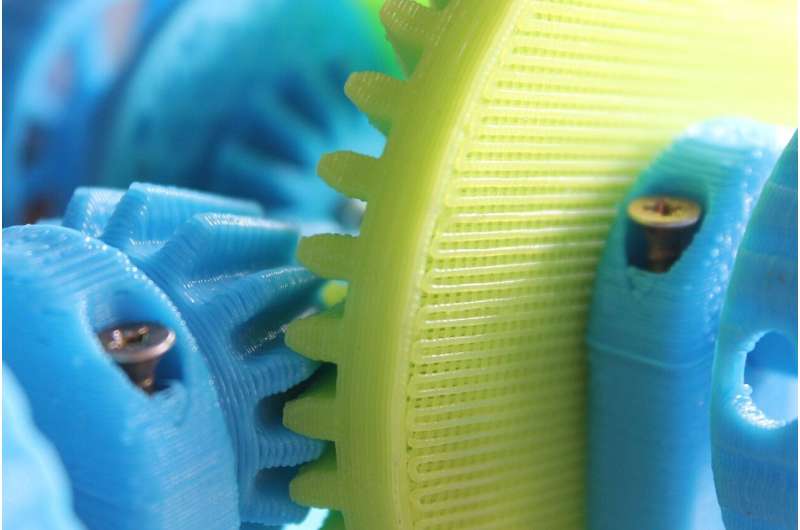
3D printers could quickly get higher at producing intricate metallic and plastic elements, due to new software program developed on the College of Michigan that reduces dangerous warmth buildup in laser powder mattress fusion printers.
Known as SmartScan, the software program demonstrated a 41% enchancment in warmth distribution and a 47% discount in deformations in a current research.
It is also more likely to pace the manufacturing course of in two methods: by decreasing the necessity for printers to decelerate to assist with cooling and by considerably decreasing heat-caused defects that should be corrected after printing.
Laser powder mattress fusion is a type of 3D printing utilized in aerospace, automotive and biomedical industries to fabricate elements which might be too intricate to make with typical manufacturing. It makes use of a laser to fuse layers of powdered metallic or plastic collectively. However the laser’s warmth can construct up within the delicate elements being printed, inflicting deformation and different defects.
“This drawback will get much more severe for elements with actually skinny options,” stated Chinedum Okwudire, U-M affiliate professor of mechanical engineering and corresponding writer of the paper in Additive Manufacturing. “The warmth does not have a variety of room to unfold, so you might want to be sensible about how you progress the laser round, in any other case your half will deform in actually bizarre methods.”
SmartScan tackles the issue by contemplating how warmth flows inside a given half and mapping an optimized scan sequence to restrict warmth accumulation in any given space. It analyzes the form of the half and the thermal properties of the fabric getting used, together with conductive and convective warmth switch.
Others within the area have experimented with various printing patterns to cut back warmth buildup, for instance by leaping from one space to a different or alternating between horizontal and vertical scanning instructions. However Okwudire says SmartScan is the primary answer that makes use of a thermal mannequin to optimally information the laser to distribute warmth extra evenly.
“Whenever you deliver science into it, you are able to do it in a manner that’s higher and works for even probably the most intricate elements,” Okwudire stated.
To find out the effectiveness of this primary model of SmartScan, the researchers used a laser to imprint an an identical sample on two stainless-steel plates. They used the SmartScan course of for the primary plate and switched to conventional printing patterns for the second plate. The prints made with SmartScan had been persistently much less warped and confirmed extra uniform warmth distribution in the course of the marking course of than the opposite strategies.
Primarily based on the outcomes of the experiment, the crew is assured that, with additional analysis, they’re going to have the ability to adapt SmartScan to construct full 3D elements. They plan to additional enhance the software program by factoring the fusing of metallic or plastic powder into their thermal modeling, in addition to enabling energetic updating of a scan sequence throughout printing primarily based on real-time noticed temperature measurements utilizing an infrared digital camera.
“The outcomes are very promising, and we have gotten a variety of constructive suggestions,” stated Okwudire, who has began to exhibit the software program to business companions. “We went with a easy mannequin as a result of it really works, and it really works higher than the trial-and-error approaches used at this time. We needed to focus in a route that’s sensible and actually has the possibility to make a distinction.”
The analysis was revealed in Additive Manufacturing.
Researchers design excessive warmth exchanger utilizing metallic 3D printing
Keval S. Ramani et al, SmartScan: An clever scanning strategy for uniform thermal distribution, decreased residual stresses and deformations in PBF additive manufacturing, Additive Manufacturing (2022). DOI: 10.1016/j.addma.2022.102643
College of Michigan
Quotation:
Smarter 3D printing makes higher elements quicker (2022, April 8)
retrieved 14 April 2022
from https://techxplore.com/information/2022-04-smarter-3d-faster.html
This doc is topic to copyright. Aside from any truthful dealing for the aim of personal research or analysis, no
half could also be reproduced with out the written permission. The content material is supplied for info functions solely.